City downtowns are generally referred to as concrete jungles as a result of the flats and workplace buildings that make up skylines from New York to Vancouver are usually made from — what else? — concrete.
However that may change with a push underway to construct extra tall buildings with one other materials: mass timber.
Mass timber is an umbrella class of supplies made by binding layers of wooden collectively to create bigger, stronger components like panels and beams. Proponents say it is quicker and simpler to construct with than concrete and metal, and fewer carbon-intensive as well.
If concrete and metal are the Coke and Pepsi of highrise building, mass timber has up to now been extra of a generic-brand cola. Mass timber made up only one per cent of all constructing building supplies in North America in 2022, in line with an RBC report.
However analysts count on the market to quickly develop within the years forward, and all throughout the nation, current mass-timber crops are being expanded and new ones are within the works, from B.C. and Alberta to Ontario and Nova Scotia.
There’s been a rise in large-scale constructing tasks utilizing mass timber, in any other case referred to as engineered wooden. Specialists say the fabric affords a number of advantages in comparison with metal and concrete — together with sustainability and pace. Talia Ricci explores whether or not it could possibly be a part of an answer to Toronto’s housing disaster.
“The demand is extraordinarily excessive for mass timber now,” stated Frank Gannon, director of stakeholder engagement with mass timber producer Western Archrib. He spoke with CBC Information inside a brand new, 155,000 sq. ft. facility the corporate is constructing north of Edmonton to maintain up with its rising orders.
“We’re filling capability slots about 10 months out from as we speak — so sure, the telephone’s ringing off the hook.”
The trade is getting a lift from new constructing codes that enable taller mass-timber buildings, and federal and provincial packages and insurance policies that encourage builders to make use of extra of it.
However up to now, the uptake of mass timber has been uneven throughout the nation, as some builders stay reluctant to change from tried-and-true supplies to one thing new.
And whereas a lot of the excitement round mass timber comes from its low carbon profile, some consultants disagree about how climate-friendly it actually is.
Beams and columns, flooring and partitions
The 2 most typical forms of mass timber are glue-laminated timber, or glulam, and cross-laminated timber, or CLT.
Glulam, which has been round for the reason that early twentieth century, is used to make beams and columns. CLT panels are a more moderen innovation used for flooring, roofs and partitions.
Taken collectively, the 2 supplies can function an alternative choice to concrete and metal in a constructing, stated Brian Merwin, senior-vice president with Mercer Mass Timber in Vancouver.
“CLT is the transformational materials for tall buildings,” he stated, including that a lot of the materials utilized in highrises is for the flooring. “[It’s] type of crammed that lacking hole to get us to the place we’re as we speak.”
Federal monitoring exhibits mass timber has mostly been utilized in institutional buildings, like colleges and group centres, however as extra analysis has emerged testifying to the hearth security of tall wooden buildings, current adjustments to constructing codes have opened the door to constructing increased.
In 2020, the Nationwide Constructing Code of Canada was modified to permit encapsulated mass-timber building as much as 12 storeys. Meaning mass timber parts in these taller buildings must be lined by a fire-resistant materials, like drywall.
Ontario and B.C. have gone additional, and can enable as much as 18-storey buildings.
Quicker and lighter
Constructing with mass timber carries a number of benefits, in line with structural engineer Robert Malczyk. It is quicker to work with than concrete, he stated, as a result of panels might be largely prefabricated and assembled on-site.
His personal five-storey Vancouver workplace constructing, made with mass timber, was erected in 12 days.
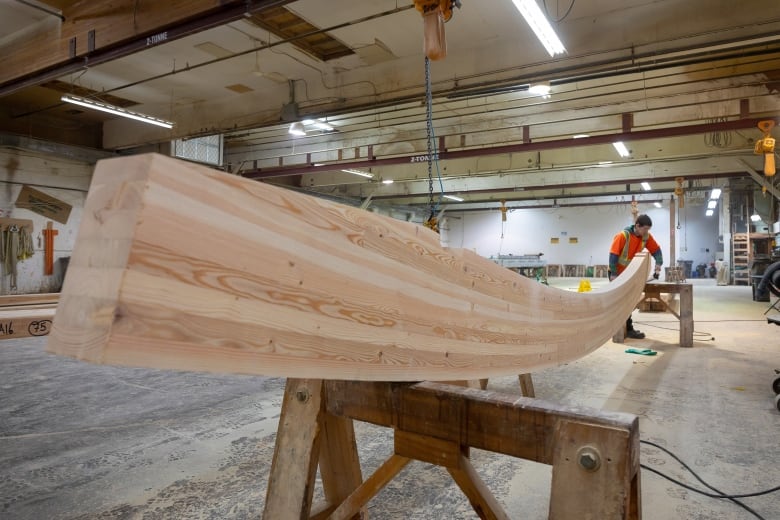
“As an proprietor, I saved loads in crane time, in closure of the streets time,” stated Malczyk, principal with the Timber Engineering consulting group.
Mass timber can also be comparatively gentle, making it extra resilient to earthquakes, he stated. Plus, many individuals merely like the way in which it seems to be.
“It has this lovely calming impact, it is a pure materials. We simply like to be surrounded by wooden.”
Proponents of mass-timber building additionally level to its environmental benefits.
Wooden is a renewable useful resource, stated Mohammad Mohammad, a senior analysis adviser with Pure Assets Canada, and producing it generates far much less carbon in comparison with metal and concrete.
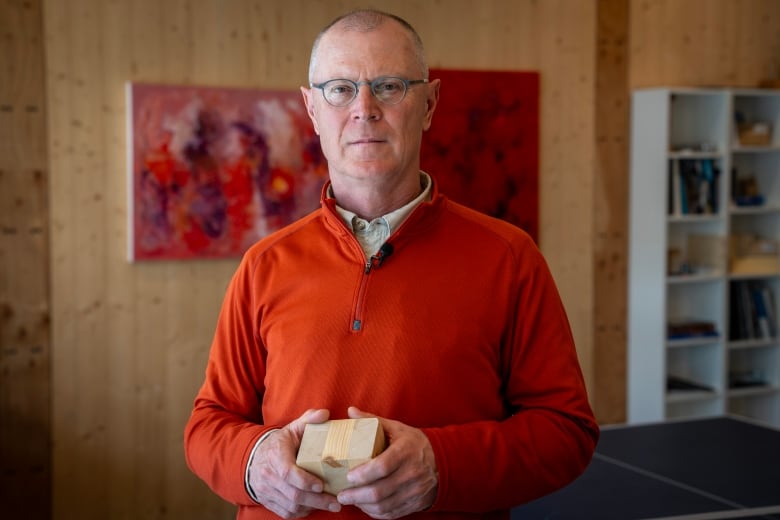
On the finish of a constructing’s lifespan, he stated, wooden will also be recycled or reused, quite than being despatched to a landfill.
“It has a variety of environmental advantages,” stated Mohammad, who works with a federal program funding modern wood-construction tasks that’s so oversubscribed, its web site accommodates a high-volume discover.
Inexperienced claims questioned
Not everybody is able to throw out their cement mixers and swap to mass timber.
Whereas building in B.C. and Quebec, for instance, has grown due to “wood-first” insurance policies of their respective provinces, different provinces stay a bit extra hesitant.
Many builders in Alberta, for instance, are learning mass timber rigorously however have not but felt comfy green-lighting a mass-timber residential constructing, stated Scott Fash, CEO of BILD Alberta.
“I feel we’re within the part of exploration and never fairly motion,” he stated.
Insurance coverage premiums will also be excessive for builders working with mass timber, stated analyst Sean Steuart, not as a result of it is a extra harmful materials however as a result of it is so new.
“It is simply not a effectively established trade, and as such, the insurance-underwriting framework is just not as effectively developed,” stated Steuart, director of fairness analysis with TD Cowen.
He stated there’s additionally a mismatch between provide and demand of mass timber: most demand is coming from Jap Canada however manufacturing is concentrated within the West, which might drive up delivery prices.
One other danger: not everybody thinks mass timber is as sustainable because it’s made out to be, and a few consultants warning in opposition to reducing down extra bushes to construct with extra mass timber.
“Probably the most beneficial factor we are able to do with forests is to depart them standing and rising,” stated Timothy Searchinger, whose work on mass timber has been printed within the journal Nature and by the World Assets Institute.
He suggests the world could be higher off exploring extra low-carbon concrete choices as an alternative.
Quicker housing building?
Mohammad, with Pure Assets Canada, stated the overwhelming majority of forests harvested in Canada are sustainable, and that normally multiple tree is planted for each one which’s lower.
As Canada makes an attempt to quickly ramp up housing building within the years forward, he believes mass timber will play an vital function within the general mixture of building supplies — particularly in Northern communities, the place concrete might be prohibitively costly and exhausting to ship.
“[You can] mainly set up a brand new housing growth inside weeks or months,” he stated.
“Now that we’re in a position to go taller and bigger with mass timber, it is simply including one other building system, one other instrument to our toolbox.”
Rick Jeffery, CEO of the Canadian Wooden Council, would not see a state of affairs the place mass timber totally replaces concrete and metal. He additionally identified that it is not frequent for buildings to be made from mass timber alone: usually they’re made from some mixture of the three supplies.
However he believes mass timber might be used rather more typically as Canada goals to construct its approach out of the housing disaster (a purpose that can require one other 3.5 million properties by decade’s finish).
“We see there is a massive alternative on that residential aspect.”